Gibson Garage x Auburn IND
“Frethaus”
Old Reserve
A small Intro…
The purpose of this project was to work along side Gibson’s master luthier, director of product development, and Auburn University School of Industrial and Graphic Design’s Professor of Practice, Keith Medley to design and fabricate our very own functioning electric guitar, going through the high end craft process of making the instrument for the Auburn University sponsored studio: Frethaus
Drawing inspiration
Looking at Gibson and its history, there were a plethora of great craft motifs to draw from and add a challenging element to the design.
The most recognizable guitar body shape that Gibson produces, the legendary Les Paul has stood the test of time being used by a variety of different artists of all genres. It is the electric guitar.
The Les Paul
Sunburst
A process where the edges of the guitar are scorched, slowly blending into the wood of the body on the face. This creates a gradient effect going across the main face of the guitar, adding a striking visual to the striking sound.
Wood Grain
While lots of guitars will simply cover up the wood they are made of with paint, other guitars utilize the beauty of their natural wood grain to emphasize the visual aspect of such an incredible instrument.
Initial Mood board
Now to add some personal flare to things. What kind of music should this guitar be meant to play? What artists should want to have this in their collection?

Sketching
3D Modeling
Time for the solo
The bulk of the work for the project was construction. With something requiring as high a level of craft as a guitar, the fabrication process is of utmost importance.
Initial CNC Prototyping
With the start of the model making process under way, CNC files were produced to make initial prototypes out of foam.
Bolt-on Neck: The neck is placed into the body slot in a more simple manner and is bolted on through the back making it detachable for travel.
VS
Set Neck: Placement of the neck in a slot on the body where the neck is glued into place. The hard way of doing things, but is standard for this body type.
Woodworking
This is where things get complicated. With woodworking, every little cut matters.
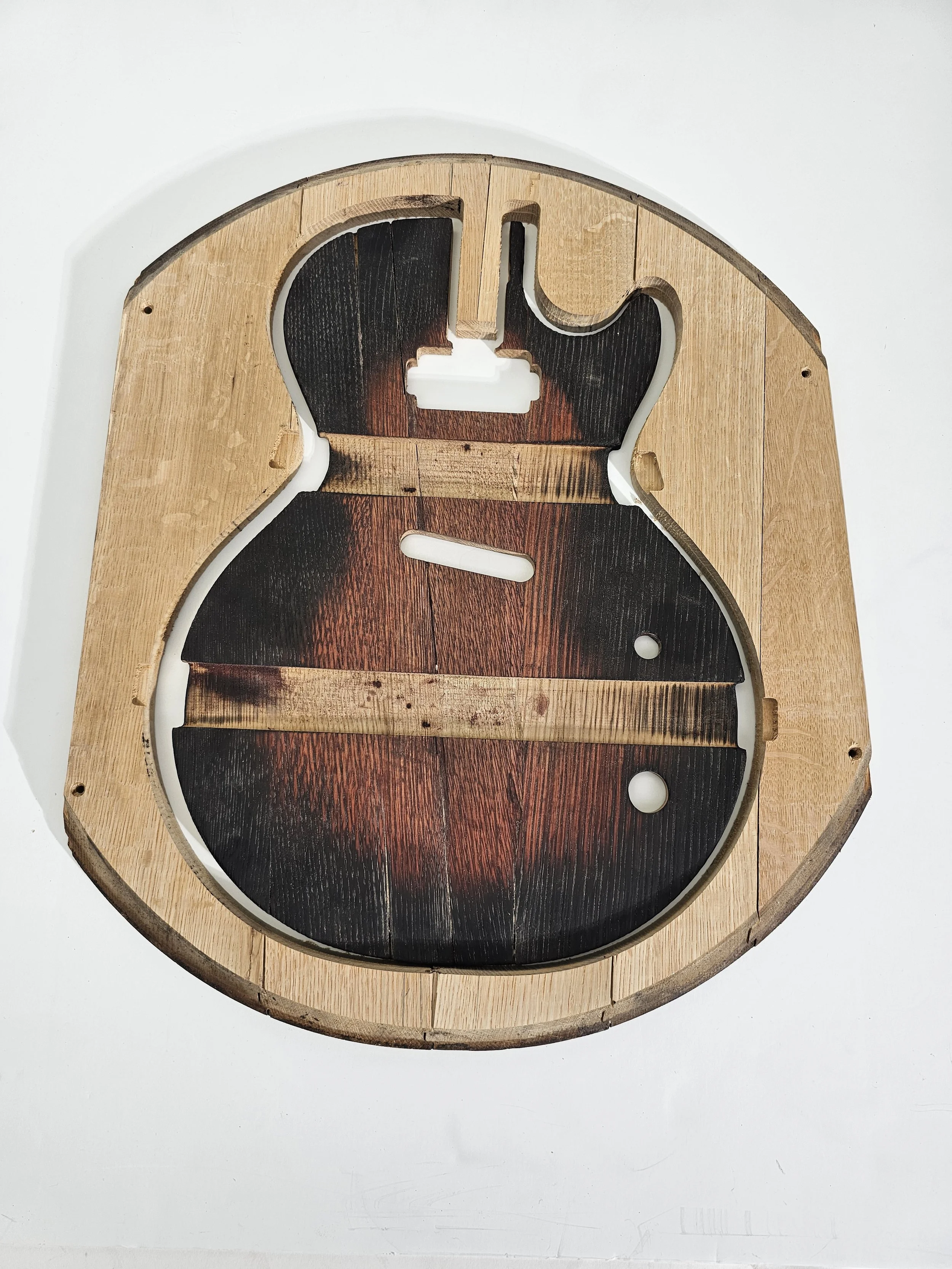
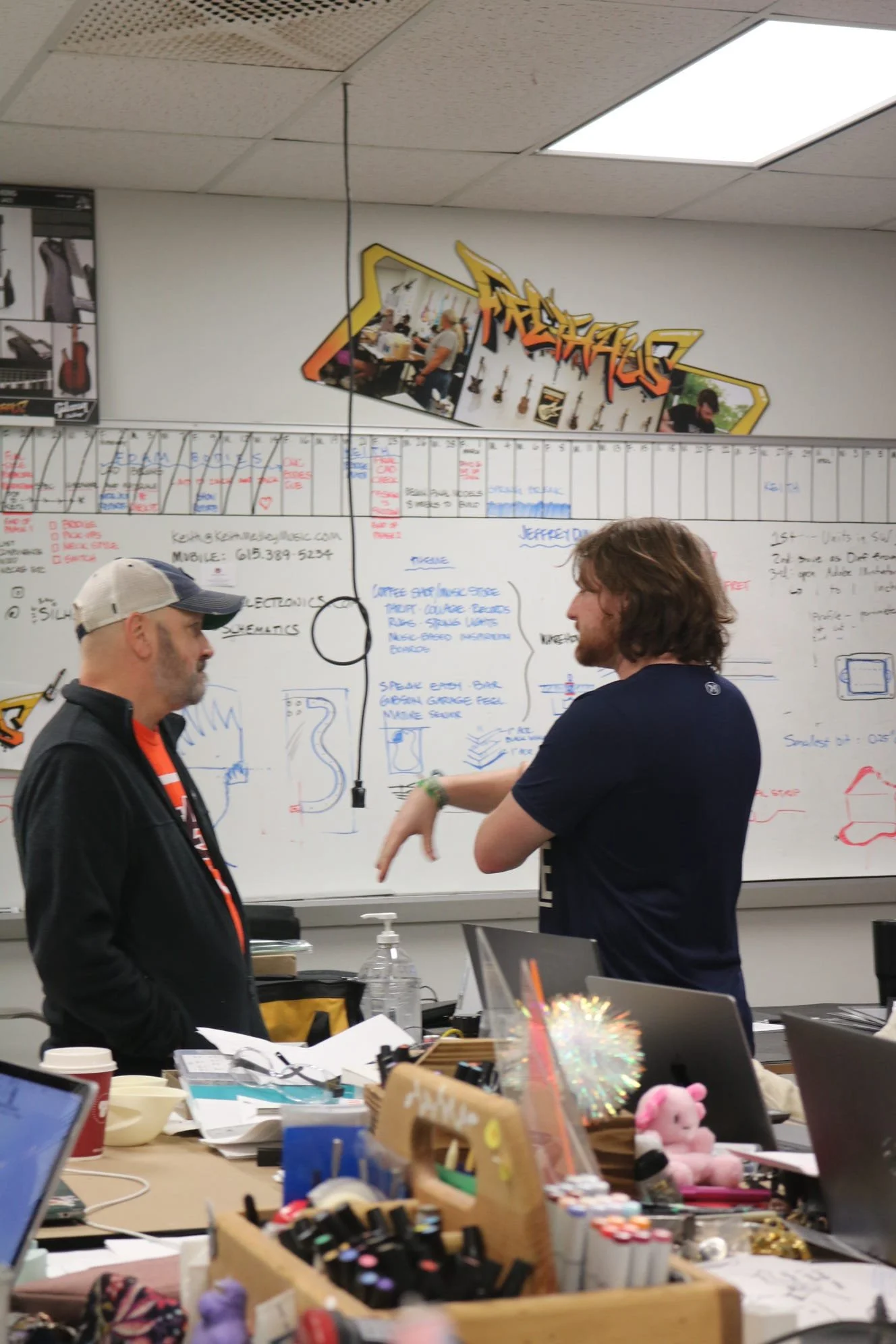
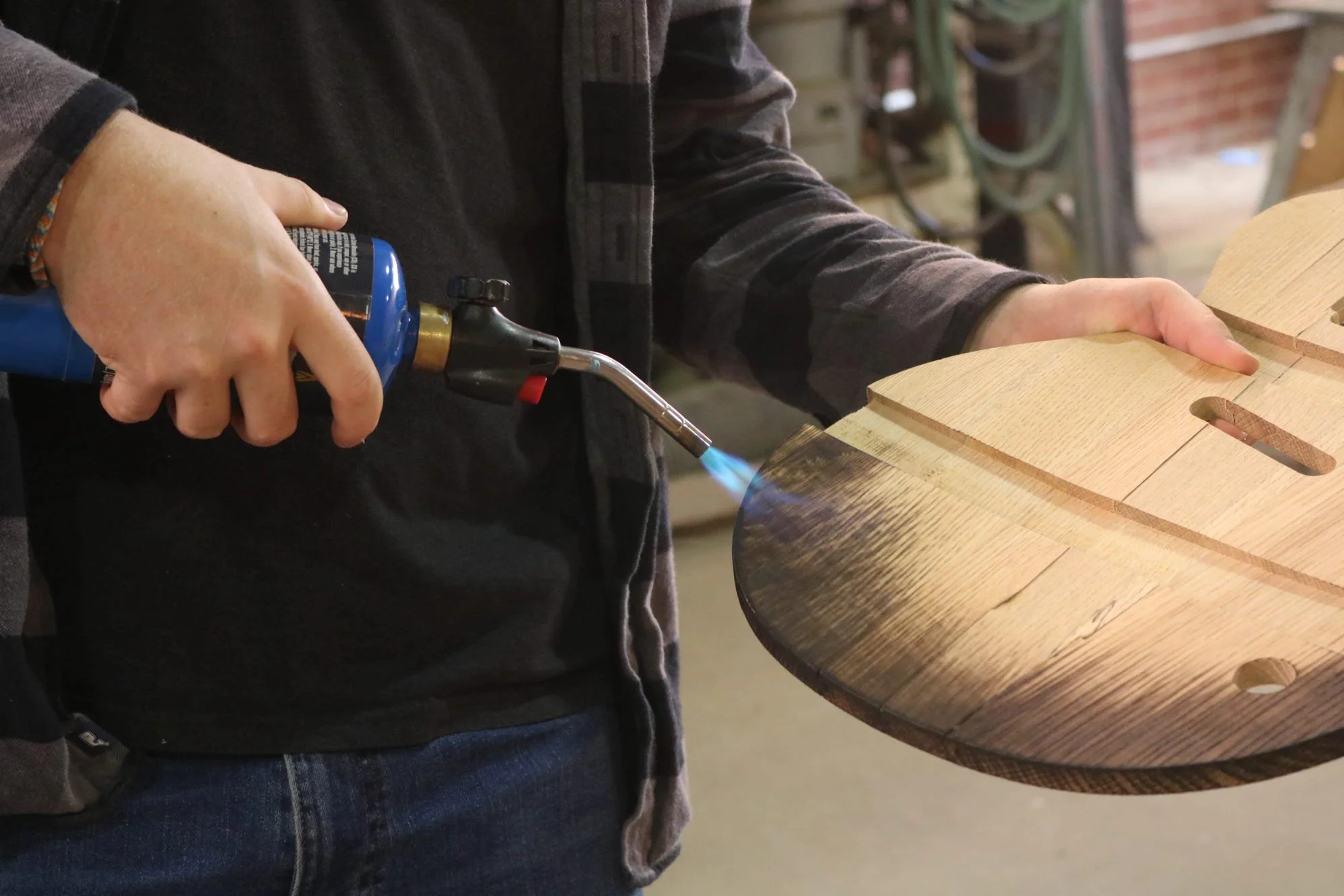
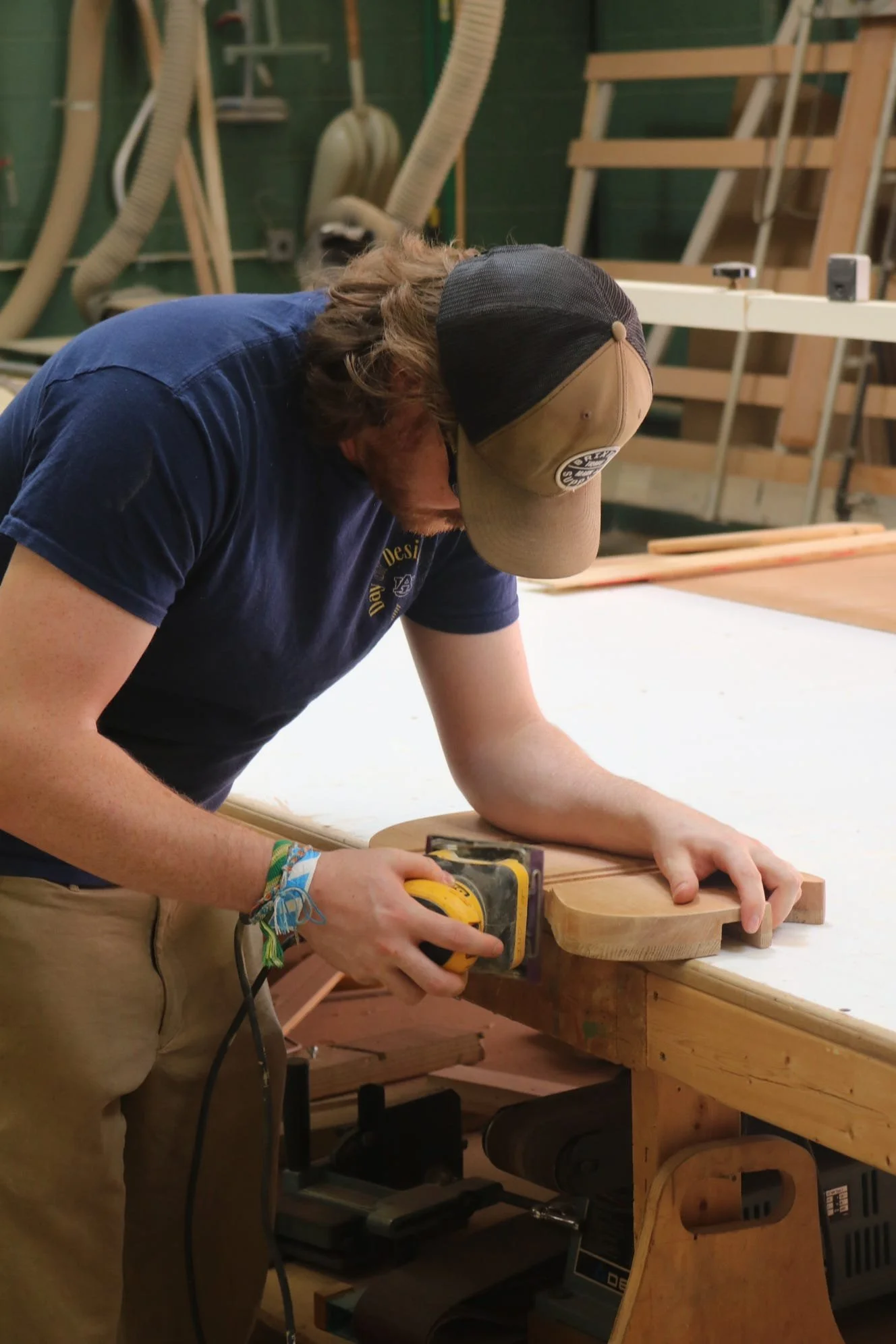

Sunbursting
A tricky process without knowing exactly what the wood stain would do, so test runs (like the one shown) were necessary. Issues involving wood bowing, cracks, and sanding issues came up, but were addressed in the final model.
Special Tuners
A certain model of Gibson tuners were taken and modified to have these spherical wooden tuning knobs to match the wood of the guitar. In hindsight, spheres should have been changed to small discs for easier stringing/ tuning.